At the University of Colorado Boulder, Component Design is one of the most important courses for Mechanical Engineering students. We are tasked with designing, building, and testing a drill-powered bicycle. At the end of the semester, teams of five compete to determine who had the quickest and most efficient design. As Systems Engineer, I assisted in creating SolidWorks parts and drawings, aided in bicycle assembly, manufactured the seat and executed the seat and frame integration, as well as designed and implemented the drive train system. Once completed, this was the final product:
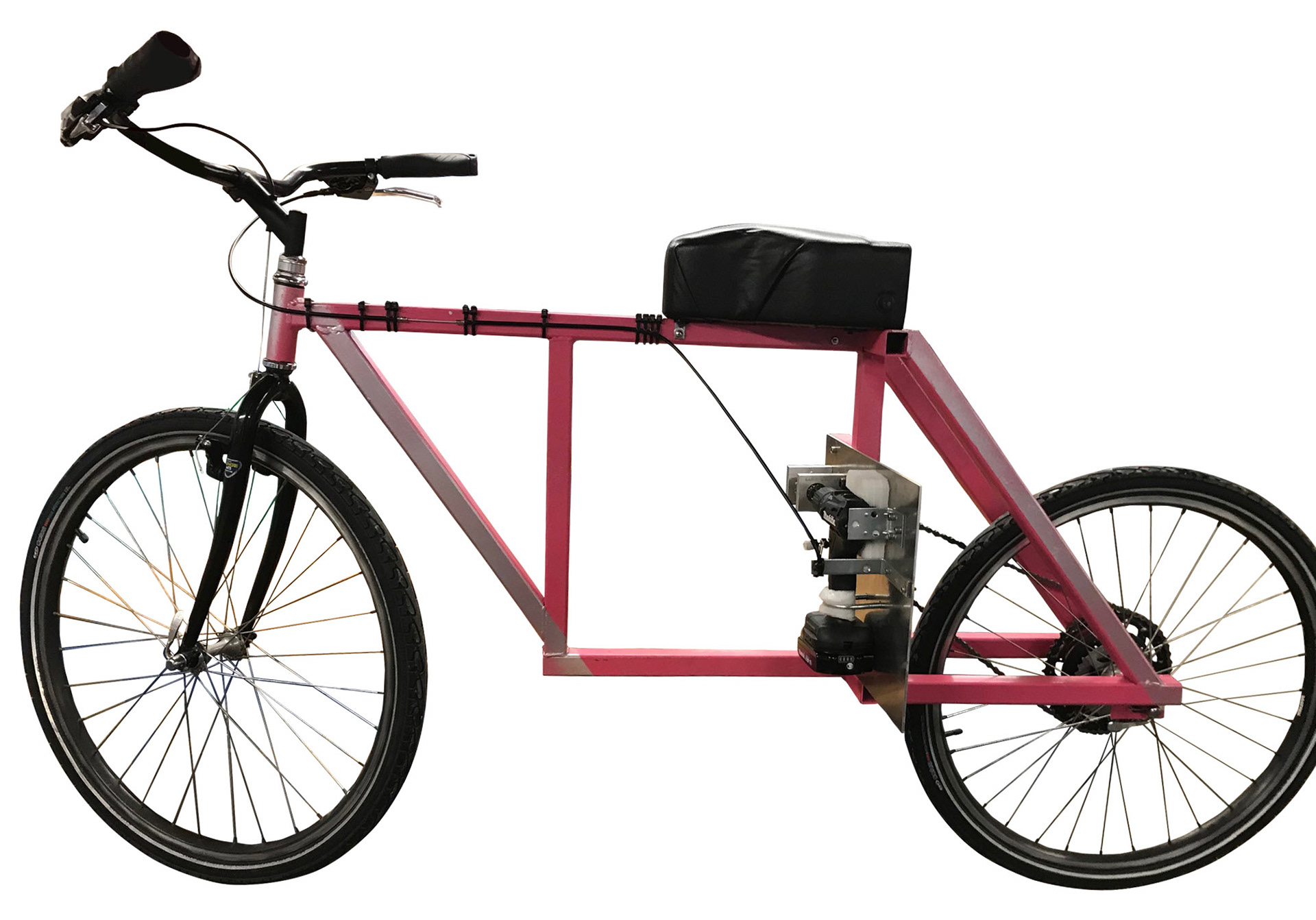
The drivetrain was actuated by the rear brake cable. When activated, a horizontal, tensile force was applied to a spring mechanism that pushed against the trigger of the drill. This way, once the rear brake lever is released, the drill will no longer run. To ensure the gear ratio was adequate to climb the required gradient with a 170-pound driver, an adapter was made to add a 48 tooth chainring to the rear cassette. The chainring was attached to the adapter using chain ring bolts. This is how the drive train functioned when completed:
The design of the seat presented many interesting opportunities. I manufactured the seat with a removable LED display and added cushion. The LED display is dynamic and increases the bicycles visibility. The lights are programmed using Arduino. Therefore, the programming can be updated and customized at any time. Currently, it fades from red to blue to red in an endless loop. An on/off switch was added on the side of the seat for user-friendliness.
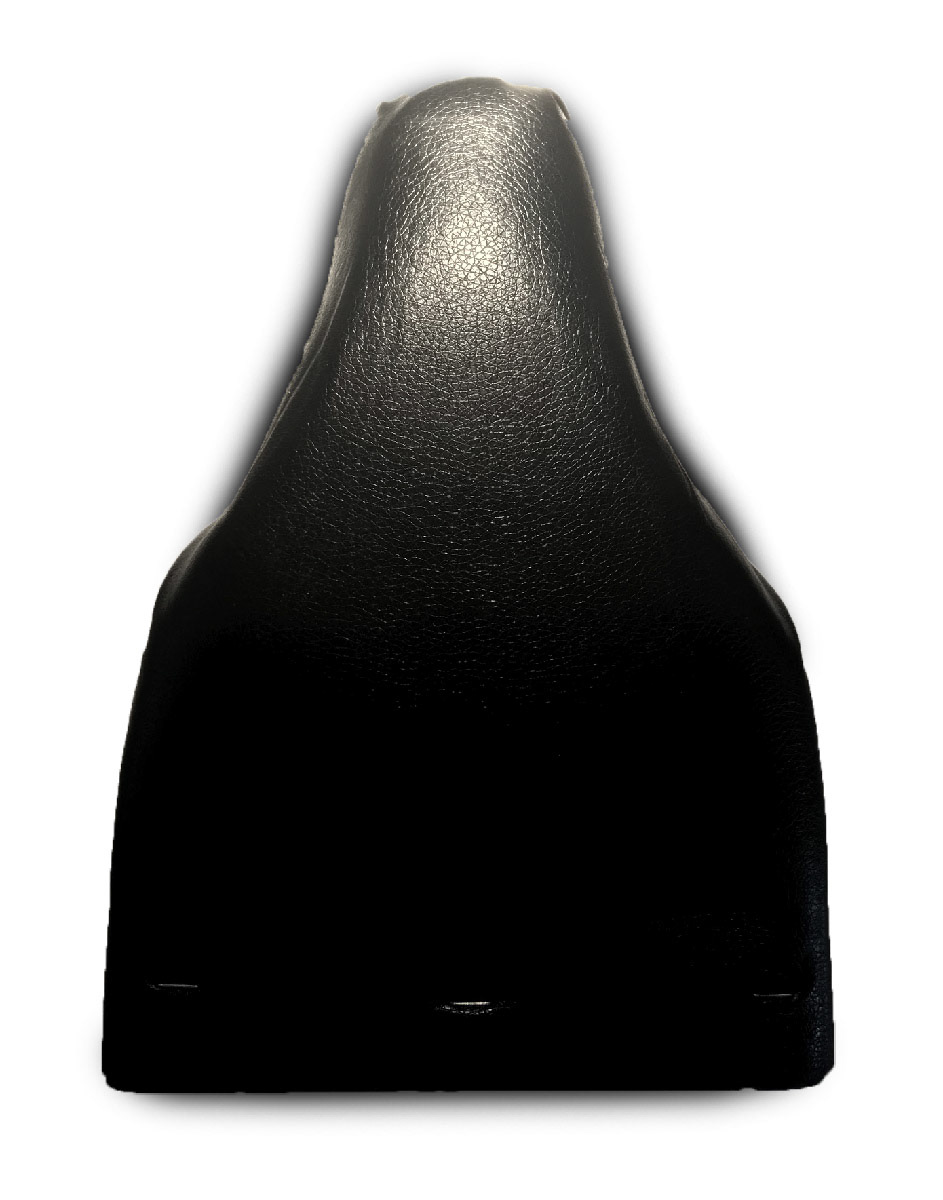
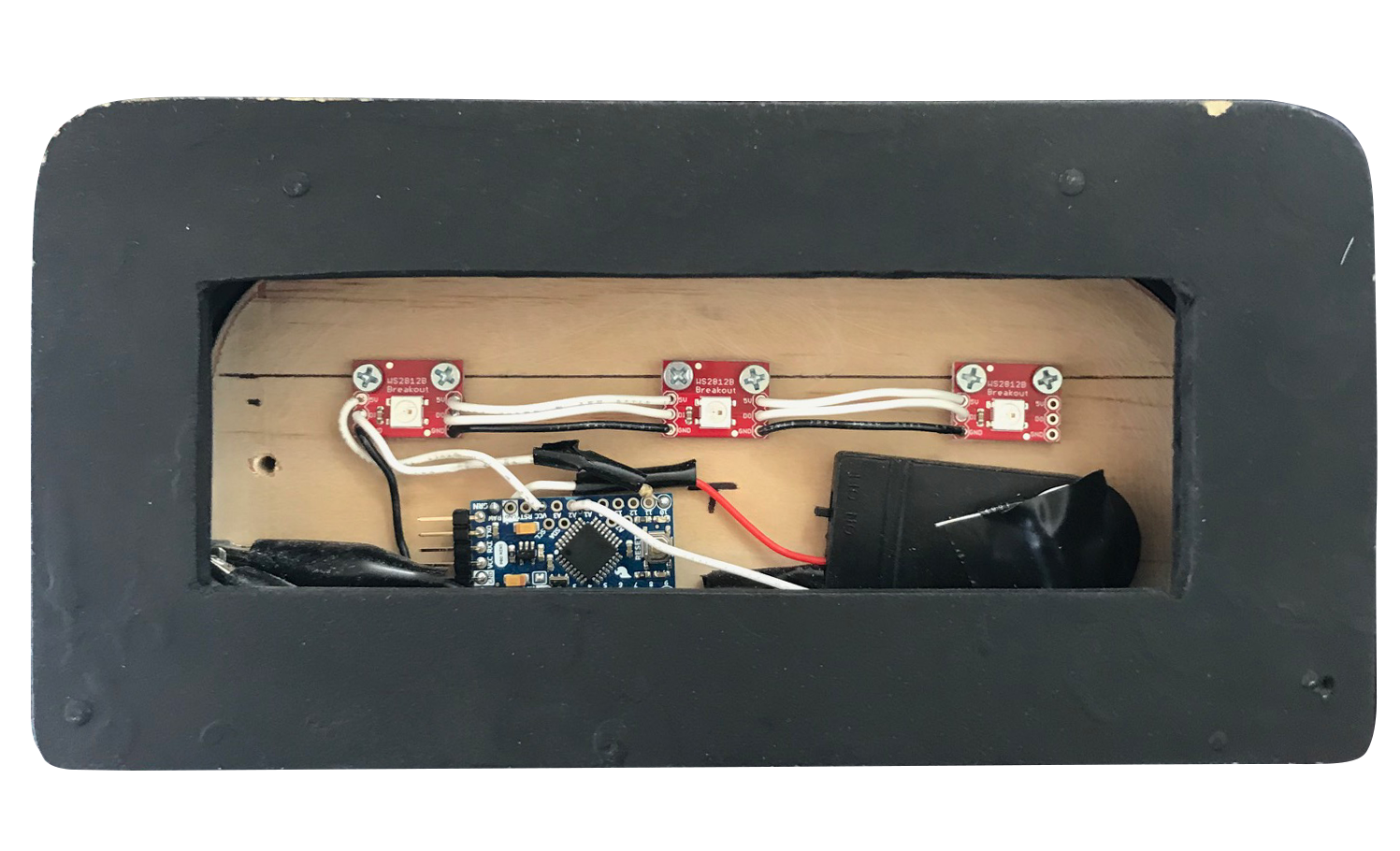
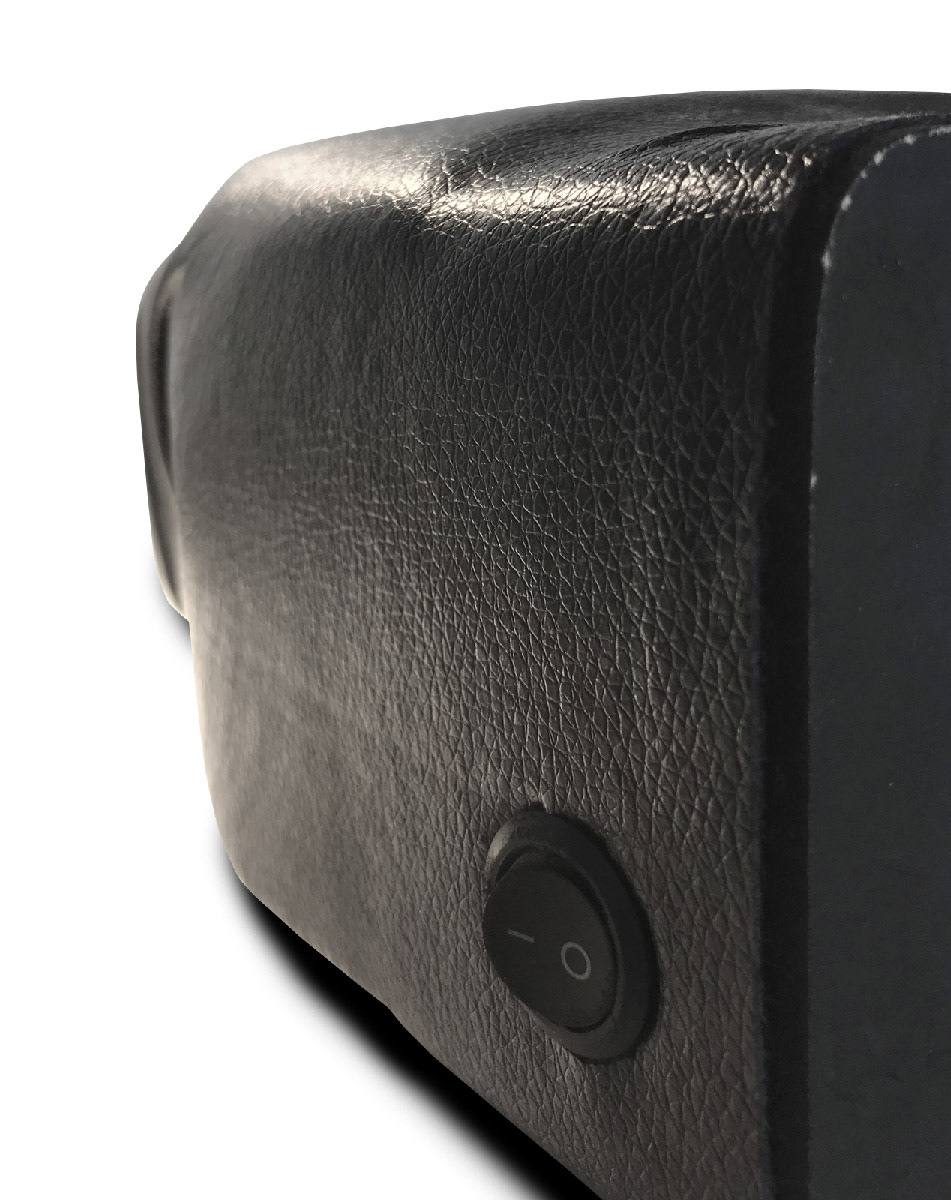
Here is the display in action: